Understanding the DMAIC Methodology: A Key to Process Improvement

Six Sigma is a methodical strategy that employs the DMAIC methodology to optimize business processes. The five essential steps of this methodology are defining, measuring, analyzing, improving, and controlling for effectiveness.
A crucial procedure for Lean Six Sigma, which is extensively used to promote improvement in numerous industries
Key Benefits of the DMAIC Process
● Better Output: Organizations save time, reduce waste, and streamline operations with the DMAIC approach.
● Data-Driven Decisions: Data analysis enables companies to identify the underlying causes of process waste and implement appropriate fixes.
● Quality Success: Take the 6 Sigma approach of DMAIC to increase product & service quality with fewer defects.
● Cutting Costs: Reducing inefficiencies will lower operating expenses, which will boost a business's profitability.
● Customer Satisfaction: DMAIC will result in improved goods and services, which will raise customer satisfaction levels.
The Five Phases of the DMAIC Model
● Define: Identify the problem, objectives, and goals of the improvement process.
● Measure: Collect relevant data to understand the current process performance.
● Analyze: Examine data to determine root causes of inefficiencies or defects.
● Improve: Develop and implement solutions to optimize the process.
● Control: Maintain improvements through continuous monitoring and adjustments.
Why Use DMAIC in Lean Six Sigma?
● Given that waste reduction and value optimization are the fundamental principles of Lean Six Sigma, DMAIC also works well with Lean.
● Enables the setting of strong business standards while also streamlining procedures.
● It is easier to develop and maintain improvements when you use a structured technique like DMAIC.
Common Applications of DMAIC and Six Sigma
● Manufacturing: Reducing defects and improving production efficiency.
● Healthcare: Enhancing patient care and reducing medical errors.
● Finance: Improving accuracy in financial transactions and reporting.
● Retail: Optimizing inventory management and customer service processes.
● IT and Software Development: Increasing efficiency in project management and software deployment.
Conclusion
For businesses looking to increase productivity, quality, and customer satisfaction, DMAIC is an essential tool. Businesses can achieve future success and ongoing improvements by implementing the DMAIC for Lean Six Sigma. To explore a detailed breakdown of this methodology, visit Sprintzeal’s blog on DMAIC methodology.
What's Your Reaction?
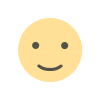
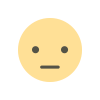
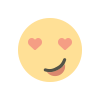
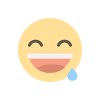

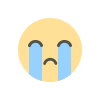
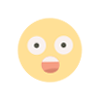