The Impact of Aluminum Molds on Sustainable Injection Molding
As industries strive to achieve greater sustainability, aluminum molds for injection molding have become an essential component in eco-friendly manufacturing.

Sustainable manufacturing has become a critical focus for industries worldwide, particularly in plastic production. Injection molding, one of the most common plastic manufacturing processes, plays a crucial role in this sustainability effort. Traditional steel molds have long been used for injection molding, but they often require extensive energy and material consumption, leading to significant environmental concerns.
Aluminum molds for injection molding have emerged as a viable alternative, providing a more sustainable solution. Their lightweight nature, faster cycle times, and recyclability make them a key component in achieving eco-friendly production processes. As industries shift towards greener solutions, the adoption of aluminum molds continues to grow, proving their value in sustainable injection molding.
Energy Efficiency and Reduced Carbon Footprint
One of the primary benefits of aluminum molds for injection molding is their ability to improve energy efficiency. Compared to steel molds, aluminum molds require less heat and cool faster, leading to lower energy consumption. This reduction in energy usage translates directly into a smaller carbon footprint, making aluminum molds an environmentally responsible choice for manufacturers looking to minimize their impact.
Additionally, aluminum molds contribute to sustainability by requiring less material to produce. Unlike traditional molds, which demand large amounts of steel, aluminum molds are lightweight and consume fewer raw materials. The lower material requirements not only reduce production costs but also decrease the overall environmental impact associated with mold manufacturing.
Faster Production Cycles and Waste Reduction
The efficiency of aluminum molds extends beyond energy savings. They also contribute to sustainable injection molding by enabling faster production cycles. Due to their superior thermal conductivity, aluminum molds allow for quicker heating and cooling times, reducing the overall production time per part. This efficiency leads to lower operational costs and less energy expenditure, aligning with sustainability goals.
Moreover, aluminum molds help minimize waste by reducing defects in molded parts. Their ability to maintain stable temperatures results in more consistent product quality, decreasing the likelihood of defective or rejected parts. This reduction in waste contributes to sustainability by lowering the amount of discarded plastic materials, further enhancing the environmental benefits of aluminum molds for injection molding.
Recyclability and Eco-Friendly Material Usage
Recyclability is a key factor in sustainable manufacturing, and aluminum molds excel in this area. Unlike steel molds, which often end up as industrial waste, aluminum molds can be easily recycled and repurposed. This ability to be melted down and reused reduces the demand for virgin materials, decreasing the environmental impact of mold production.
Furthermore, aluminum is a highly sustainable material due to its abundance and recyclability. Manufacturers can incorporate recycled aluminum into their mold-making processes, further reducing the need for new material extraction. By integrating recycled aluminum into injection molding, companies can support circular economy initiatives and promote a more sustainable manufacturing ecosystem.
Cost Savings and Long-Term Sustainability
While initial investments in aluminum molds for injection molding may seem comparable to steel molds, their long-term cost savings make them a financially sustainable option. The reduced energy consumption, faster cycle times, and lower maintenance requirements contribute to significant operational savings. These financial benefits make aluminum molds an attractive choice for companies aiming to balance sustainability with cost-efficiency.
Additionally, the durability and longevity of aluminum molds ensure prolonged use without frequent replacements. Their resistance to corrosion and ability to maintain performance over time mean fewer resources are needed for mold maintenance and replacement. By investing in aluminum molds, manufacturers can achieve sustainable injection molding practices while benefiting from long-term cost-effectiveness.
Conclusion
As industries strive to achieve greater sustainability, aluminum molds for injection molding have become an essential component in eco-friendly manufacturing. Their ability to improve energy efficiency, reduce waste, enhance recyclability, and lower production costs makes them a superior alternative to traditional steel molds. By adopting aluminum molds, manufacturers can contribute to a more sustainable future while maintaining high production standards.
Looking ahead, advancements in aluminum mold technology will continue to drive innovation in sustainable injection molding. With increasing emphasis on reducing environmental impact and optimizing resource utilization, aluminum molds will play a crucial role in shaping the future of plastic manufacturing. Companies that embrace this shift will not only benefit from improved efficiency but also position themselves as leaders in sustainable production practices.
What's Your Reaction?
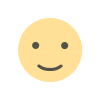
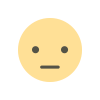
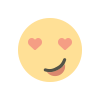
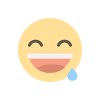

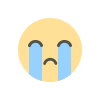
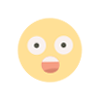