How Much Do Pre-Engineered Metal Buildings Cost?
Learn about the cost factors of pre-engineered metal buildings, including material, size, and customization, to help you plan your next construction project.

Pre-engineered metal buildings (PEMBs) are a popular and cost-effective option for commercial, industrial, agricultural, and residential construction projects. These buildings offer several benefits, including durability, energy efficiency, and quick installation, but understanding the cost is a crucial aspect of planning your project. The total cost of a pre-engineered metal building can vary greatly depending on several factors. In this post, we’ll break down what influences the prefabricated buildings prices and provide a general idea of what you can expect to pay.
1. Size of the Building
The size of your pre-engineered metal building is one of the most significant cost factors. The larger the building, the more materials and labor will be required, leading to higher costs. Costs are typically quoted per square foot, so the bigger the space, the higher the price.
- Small Buildings (Up to 1,500 sq ft): Small residential, storage, or workshop PEMBs may cost between $10,000 and $30,000, depending on other factors like materials and design.
- Medium Buildings (1,500 to 5,000 sq ft): A medium-sized commercial building or warehouse could range from $30,000 to $75,000.
- Large Buildings (Over 5,000 sq ft): Larger PEMBs for industrial or agricultural use can cost anywhere from $75,000 to $250,000 or more.
2. Materials Used
The materials chosen for the building will significantly influence the cost. Steel is the most common material used for pre-engineered metal buildings because it’s strong, durable, and relatively affordable. However, there are variations in steel quality, coating, and finish, which can add to the cost.
- Steel Quality: Higher-grade steel or corrosion-resistant steel may increase the overall price.
- Roofing and Wall Panels: The type of panels (galvanized, insulated, or corrugated) used for the roof and walls will impact the cost. Insulated panels, for example, are more expensive than non-insulated ones but provide better energy efficiency.
- Coatings and Finishes: Specialized coatings, like those for corrosion protection or enhanced aesthetics, will add to the price.
3. Design and Customization
Pre-engineered metal buildings can be customized to fit specific needs and preferences, but the more customized the design, the higher the cost. Factors such as architectural complexity, special openings, and additional features (like windows, doors, insulation, or skylights) can drive up the price.
- Complexity of Design: A simple rectangular building will cost less than one with more intricate design features, like a sloped roof or non-standard shapes.
- Customization Options: If you need custom doors, windows, or finishes, these will increase the cost. Additionally, specific design requirements, like larger clear spans or higher roofs, will also affect the price.
4. Location and Site Preparation
The location of the building site plays a role in its overall cost. Areas with difficult terrain or challenging weather conditions may require additional site preparation, such as excavation, grading, or foundation work. The accessibility of the site can also impact the cost of delivery and installation.
- Foundation: Most PEMBs require a concrete foundation, which can add several thousand dollars to the total cost. The type of foundation required will depend on factors like soil condition and building size.
- Shipping and Transportation: If your site is remote or hard to access, transportation costs for the metal components may increase.
5. Labor and Installation Costs
While PEMBs can be installed more quickly than traditional buildings, labor costs still play a significant role in the overall price. Professional contractors or builders with experience in metal buildings will likely charge more for their expertise, but using them can reduce the risk of errors or delays.
- Installation Labor: Depending on the complexity of the build, installation costs can range from $5,000 to $15,000 or more.
- DIY vs. Professional Help: If you choose to install the building yourself, you can save on labor costs, but it will require more time, tools, and expertise.
6. Additional Features and Upgrades
Pre-engineered metal buildings can be fitted with various additional features and upgrades that can impact the total cost. Some of the most common upgrades include:
- Insulation: Insulating your PEMB will add to the initial cost but can lead to long-term energy savings. Insulation is typically applied to the roof and walls and can range from $1 to $3 per square foot.
- Ventilation: Proper ventilation systems, including windows, roof vents, or fans, may be necessary depending on the building's intended use. Adding these features will increase the overall cost.
- Climate Control Systems: If the building needs heating, cooling, or dehumidifying systems, this will also add to the cost. These systems are particularly important in commercial and industrial applications.
- Safety Features: Fire suppression systems, security systems, and other safety upgrades will increase the price.
7. Total Cost Estimates
To give you a rough idea, here are some estimated costs for various types of pre-engineered metal buildings:
- Small Storage or Workshop Building (Up to 1,500 sq ft): $10,000 to $30,000
- Medium Commercial Building (1,500 to 5,000 sq ft): $30,000 to $75,000
- Large Industrial or Agricultural Building (5,000 sq ft and beyond): $75,000 to $250,000 or more
These estimates are for the basic shell of the building and do not include additional features like insulation, interior finishes, or site preparation.
Conclusion
The cost of a pre-engineered metal building can vary widely based on the size, materials, design, location, and additional features. While they may initially cost more than traditional wood or brick buildings, the long-term savings in energy efficiency, durability, and maintenance make PEMBs an attractive option for many projects. To get an accurate estimate for your specific needs, it’s best to consult with a reputable manufacturer or contractor who can provide a detailed quote based on your requirements.
What's Your Reaction?
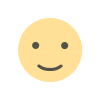
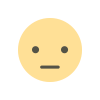
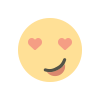
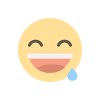

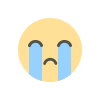
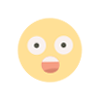