How Can You Prevent a Coolant Hose from Bursting?
A coolant hose is essential for regulating your engine's temperature, and a burst hose can lead to overheating and costly repairs.

A coolant hose burst can lead to severe overheating and potential machine damage. The coolant hose is a crucial component of a machine’s cooling system, responsible for circulating coolant between the radiator and other cooling parts to maintain an optimal operating temperature. A properly functioning coolant hose improves machine efficiency, extends component lifespan, and prevents costly repairs. Routine inspection and maintenance are essential to prevent sudden coolant hose burst, which can cause unexpected failures. Understanding the causes of coolant hose failure and taking preventive measures can help guarantee the smooth operation of your machinery.
Importance of a Coolant Hose in a Machine’s Cooling System
If a coolant hose bursts, it can lead to sudden coolant loss, causing the engine or machine to overheat rapidly. The coolant hose plays a vital role in regulating temperature by allowing the continuous flow of coolant, preventing overheating by transferring excess heat to the radiator for dissipation. A high-quality coolant hose ensures consistent performance, minimizes leaks, and protects the machine from thermal damage. Without a properly functioning hose, overheating can cause severe mechanical issues, reduced fuel efficiency, and potential breakdowns. Regular maintenance and timely replacement of worn-out hoses help prevent coolant hose bursts and keep the cooling system efficient.
Consequences of a Burst Coolant Hose
A burst coolant hose can lead to severe machine problems, including overheating and potential machine failure. When a hose fails, coolant leaks out, reducing the system’s ability to regulate temperature. This can result in extreme heat buildup, leading to machine damage, warped cylinder heads, or blown head gaskets. Additionally, coolant leaks can cause slippery surfaces, increasing the risk of accidents. In extreme cases, continued operation with a burst hose may lead to complete machine seizure, requiring expensive repairs or replacement. Addressing coolant hose issues promptly can prevent these costly consequences and ensure the longevity of the machine.
Understanding the Causes of Coolant Hose Failure
- Age and Wear of the Hose
Over time, coolant hoses deteriorate due to continuous exposure to heat, pressure, and coolant chemicals. Aging hoses develop cracks, become brittle, and lose flexibility, increasing the risk of failure.
- High machine Temperatures and Overheating
Prolonged exposure to high temperatures weakens hose materials, making them prone to cracking and bursting. Overheating exacerbates wear and accelerates hose degradation.
- Incorrect Coolant Type or Contamination
Using the wrong coolant or failing to replace it regularly can lead to chemical buildup and hose degradation. Contaminants in the coolant can cause internal corrosion and weakening of the hose structure.
- Loose or Damaged Hose Clamps
Loose clamps can cause leaks, while overtightened clamps may damage the hose, leading to premature failure. Regular inspection of clamps is crucial to maintaining a secure connection.
- External Damage from Debris or Contact with machine Parts
Hoses that rub against sharp edges or moving machine components can suffer abrasions or punctures. Ensuring proper routing and securing of hoses can prevent such damage.
Regular Inspection and Maintenance
Regular inspection and maintenance are essential to prevent coolant hose failure and ensure the cooling system functions optimally.
- Checking for Cracks, Bulges, and Soft Spots
Inspect hoses visually and by touch to identify symptoms of wear, such as cracks, bulges, or soft areas. These indicate structural weaknesses that can lead to failure.
- Ensuring Clamps are Secure and Not Corroded
Loose or corroded clamps can cause leaks and compromise the integrity of the cooling system. Tighten or replace clamps as needed to ensure a secure fit.
- Flushing and Replacing Coolant Periodically
Regular coolant changes prevent buildup of contaminants that can degrade hoses. Flushing the cooling system removes debris and extends the lifespan of hoses.
Choosing High-Quality Hoses and Clamps
- Selecting the Right Hose Material (Rubber vs. Silicone)
Rubber hoses are cost-effective and suitable for most machines, while silicone hoses offer better heat opposition and longevity, creating them ideal for high-performance applications.
- Importance of OEM or High-Quality Aftermarket Hoses
OEM and high-quality aftermarket hoses ensure proper fit, durability, and performance. Avoid low-quality alternatives that may fail prematurely.
- Using Proper Clamps to Prevent Leaks
Invest in high-quality clamps that provide secure, leak-free connections. Stainless steel clamps resist corrosion and ensure a longer service life.
Avoiding Overheating and Coolant System Issues
- Monitoring machine Temperature Regularly
Keep an eye on the temperature gauge to detect early signs of overheating. Address any abnormal readings immediately.
- Maintaining Proper Coolant Levels
Inspect coolant levels frequently and top up as needed to prevent air pockets and overheating issues.
- Ensuring the Radiator and Thermostat Function Properly
A malfunctioning radiator or thermostat can cause coolant circulation problems. Regularly inspect and replace faulty components.
Proper Installation of Coolant Hoses
- Ensuring Correct Fit and Alignment
Hoses should be properly aligned and securely attached to avoid leaks and premature wear.
- Using Recommended Torque Settings for Clamps
Overtightening clamps can damage hoses, while loose clamps can cause leaks. Follow manufacturer torque specifications for best results.
- Avoiding Excessive Bending or Twisting of the Hose
Improper routing and excessive bending can weaken the hose structure. Ensure hoses are installed in a way that minimizes stress.
Signs of a Failing Coolant Hose
- Visible Cracks or Leaks
Inspect hoses for visual signs of damage, such as cracks, fraying, or coolant seepage.
- Steam or Overheating Issues
A sudden increase in machine temperature or visible steam from the machine bay may indicate a failing coolant hose.
- Low Coolant Levels or Coolant Puddles Under the industry
Unexplained drops in coolant levels or puddles beneath the machine suggest a leak that requires immediate attention.
Conclusion
Coolant hoses are essential for maintaining machine temperature and preventing overheating. Regular assessment, maintenance, and timely replacement of hoses provide the longevity and efficiency of the cooling system. Choosing high-quality hoses and clamps, following proper installation procedures, and monitoring coolant levels help prevent sudden failures. Addressing signs of wear and potential issues early can save costly repairs and keep your machinery running smoothly. Proteus Industries Inc. offers reliable cooling solutions to enhance system performance and durability. Prioritizing the health of your coolant hoses is a simple yet critical step in ensuring optimal machine performance and reliability.
What's Your Reaction?
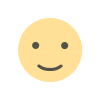
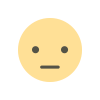
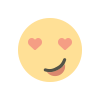
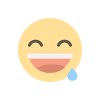

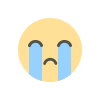
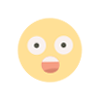