Advanced Precision CNC Machining for High-Quality Parts
In the medical sector, precision CNC machining is crucial for manufacturing implants, surgical instruments, and diagnostic equipment.
Precision CNC machining is a cornerstone of modern manufacturing, enabling the production of high-quality parts with exceptional accuracy. By leveraging computer numerical control (CNC) technology, manufacturers can create complex components with tight tolerances, reducing human error and increasing efficiency. This process is widely used across various industries, including aerospace, automotive, medical, and electronics, where precision is critical to performance and safety.
The demand for precision CNC machining has grown significantly as industries strive for higher standards and tighter specifications. With advancements in CNC technology, manufacturers can achieve micron-level precision, ensuring that each part meets the exact requirements. This not only improves product performance but also enhances reliability and longevity, making CNC machining an indispensable tool in modern production.
The Role of CAD and CAM in Precision CNC Machining
Computer-aided design (CAD) and computer-aided manufacturing (CAM) software play a vital role in precision CNC machining. CAD software allows engineers to design intricate components with high accuracy, ensuring every detail is accounted for before production begins. These digital blueprints are then translated into CNC programs that guide machines to execute precise cuts, drills, and shaping operations with minimal deviation.
CAM software optimizes the machining process by generating tool paths, selecting appropriate cutting tools, and determining optimal speeds and feeds. This automation enhances efficiency while reducing material waste and production time. By integrating CAD and CAM, manufacturers can streamline their operations, minimize human intervention, and produce complex parts with unparalleled precision and consistency.
Key Technologies in Precision CNC Machining
Advanced precision CNC machining relies on several cutting-edge technologies to achieve superior accuracy and efficiency. Multi-axis machining, for instance, enables machines to move in multiple directions simultaneously, allowing for intricate geometries and reduced setup times. Five-axis CNC machining, in particular, is essential for aerospace and medical applications, where complex components with tight tolerances are required.
Another critical technology is high-speed machining, which utilizes advanced spindle speeds and feed rates to enhance cutting performance. This reduces cycle times while maintaining exceptional surface finishes, making it ideal for industries that demand both speed and quality. Additionally, real-time monitoring systems and AI-powered analytics further improve CNC machining precision by detecting anomalies and optimizing machining parameters.
Benefits of Precision CNC Machining in Various Industries
Precision CNC machining offers significant advantages across multiple industries, making it a preferred choice for high-quality manufacturing. In the aerospace industry, for example, CNC machining is used to produce lightweight yet durable components that meet strict safety and performance standards. The ability to achieve tight tolerances ensures that aircraft parts fit seamlessly, reducing the risk of mechanical failures.
In the medical sector, precision CNC machining is crucial for manufacturing implants, surgical instruments, and diagnostic equipment. The high level of accuracy ensures that medical devices perform reliably, improving patient outcomes. Similarly, in the automotive and electronics industries, CNC machining enables the production of intricate parts with consistent quality, enhancing product functionality and longevity.
Future Trends in Precision CNC Machining
The future of precision CNC machining is driven by technological advancements that further enhance accuracy, efficiency, and automation. One of the most promising trends is the integration of artificial intelligence (AI) and machine learning into CNC systems. These technologies enable predictive maintenance, adaptive machining, and real-time quality control, reducing downtime and improving overall productivity.
Another emerging trend is the use of additive manufacturing in conjunction with CNC machining. Hybrid manufacturing, which combines 3D printing and subtractive machining, allows for greater design flexibility and material efficiency. Additionally, the development of advanced materials, such as composites and high-performance alloys, continues to push the boundaries of precision CNC machining, opening new possibilities for industries that demand superior performance and durability.
What's Your Reaction?
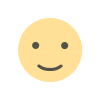
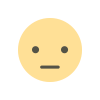
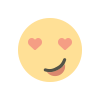
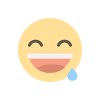

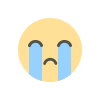
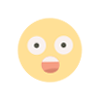